Why use BIM for Data Capture for New & Existing Buildings?
Modern Asset & Facilities Management use information about their assets to plan and maintain them in a Fit for Purpose state so that they can fulfill their space function to maximise their asset value.
To do this you require information about the buildings so that you can use predictive tools to:
- Effectively budget to maintain the buildings
- Plan cleaning regime for building & setting up contract
- Plan preventative maintenance works (
- Plan for scheduled maintenance (eg cleaning gutters late autumn)
- Plan for legislative requirements (such as checking fire extinguishers on regular basis)
- Allow for contingencies for reactive maintenance (leaking pipe in bathroom)
To do that effectively you need reasonable data on your building so that Asset Management Information System (AMIS)[*1 footnote at end of article] tools can do budget and forward planning modelling so that you can forecast major costs for planning and adjust your work regime to carry out the work in a structured and timely manner.
- Speed up the tedious stuff and enjoy designing and documentation more
- Works in all versions of Revit
- Information to PROVE your increased speed
Having the information early means you can competitively tender the work to get the best price.
Two examples of predictive tools, where you can get an overview of Elements of your building portfolio to plan for Budgeting & when the elements need intervention are:
This visualisation lets you look at external fabric condition changing over time in the next 30 years so you have an overview of parts that need maintenance.
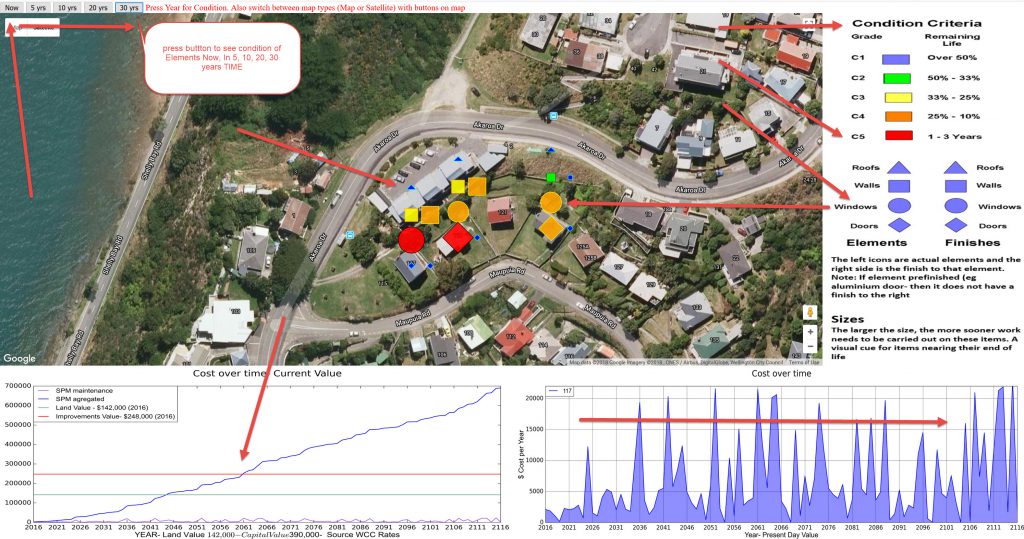
This visualisation using Excel tables lets you look at when items will need intervention over the next 42 years by filtering year by conbdition (show desc- worst to best, so what will need doing on a particular set of properties)

So how do you get information on your building portfolio?
Generally the client gets a set of As-Built documents and an Operation & Maintenance Manual for their building via the Design team who have checked that the documentation shows the changes that occurred during construction.
This documentation is not in a state that is readily transferable into an AMIS. So only some overall quantities are put into the system and the scheduling of Preventative & Scheduled systems are tagged and put in calendars for planning. Budget is done by someone estimating from historical records possible scenarios for the future and adding a contingency.Forecasting by guessing.
Gathering Accurate Information for AMIS
To make predictions an AMIS will require the following information to be captured by users:
- Element nature with a Baselife of that element ( eg paint finish- 10 years, metal roof – 40 years etc)
- Quantity of Element ( eg paint area- 1000 m2, metal roof 500 m2)
- Quality of element at a point in time. Current condition, so giving a linear scale of 1 to 10, 1 being new, 10 being needs immediate replacement ( so for paint, if condition 5, then 5 years will need replacing, for metal roof, if condition 5 also, then needs replacing in 20 years)
How would you gather information to put into your Asset Management Information System (AMIS)?
- Go on site, inspect and measure for quantity & quality and put the information into the AMIS
- Measure from plans and other docs for quantity and also survey existing condition for quality and put the information into the AMIS
- Extract from CAD plans & calculate quantity and also survey existing condition for quality and put the information into the AMIS
- Put into BIM & calculate quantity and also survey existing condition for quality and put the information into the AMIS
Why would you do this?
Maximise profits and minimise expenditure of course.
If you are a landlord, like a private developer, you just pass higher maintenance costs onto the tenants. That is fine if the building is in a prime location, there is a demand for office space and the building is not at a point where it needs high maintenance intervention (near end of life for systems and envelope). If the rents are too high, tenants will move. If maintenance gets too much, you can sell the building or demolish it to build a new building.
If you are a Government Organization that owns its own buildings and uses them then you cannot pass on costs, you are wanting to maximise the life of the buildings to keep them in a Fit for Purpose State for as long as possible, at the same time minimising expenditure on maintenance. If, say you are a university, you cannot sell the building as its on your campus at the end of its life (unless it can be relocated off site) so the only choice is to demolish and build new.
Using an example of an office building. The main cost per annum is usually salary/wages. It is the staff who are generating wealth for the company. The environ, the office space is the backdrop in which they perform their tasks. There are many examples of poor productivity and absenteeism due to poor morale and poor quality spaces (poor heating/Air conditioning, Sound issues etc).
The lack of productivity of staff will more than offset the cost of reasonable maintenance to keep the building in a Fit for Purpose state. So having a preventative maintenance regime is much better than a reactive regime as there is much more predictability of when maintenance work will generally take place and it will be far less disruptive as its planned.
From a maintenance point of view, you want to move as much of your work into the planned preventative & scheduled maintenance and away from reactive maintenance, this is more expensive as its unplanned and you need the work done immediately, so there is no tendering for lowest price.
Also regular maintenance extends the life of elements. Eg Paint systems on the outside of buildings. In AMIS modelling there is the standard base life of the element, eg paint-10 years, a Lower Base life, say 8 years (80% of the life of the system), if the system is not properly maintained (washed at intervals) and Upper Baselife, say 12 years (120% of the life of the system), if the system is maintained above average.
So between doing nothing and looking after your system well,, in this example you get a 40% difference in the life of the paint system. This difference can be balanced with:
Cost of re-painting ($x)+ [cost of maintenance (scenario- lower Baselife = $0 x Lower Base life (8 yrs) , Standard=$y x Base life(10 yrs), & Upper Baselife=$z x Upper Base Life (12 yrs))]
This should give you an indicative indication as to which strategy to take on maintaining specific elements, especially high cost, important elements related to weathertightness.
To carry out this exercise in a meaningful way the better data you have, the more accurate is your forecasting, and planning for future costs and hence budgeting requirements.
An example of effect of Different BaseLifes (Standard, Upper, Lower) on elements life is shown in the following visualisation.

Building Assets tend to be expensive, and they last a long time as in decades & decades.They are also expensive.
So capturing good information about them to be able manage them properly through their life seems to be a small cost for the benefits that can come from the collection of the data.
Generally most property portfolios are at least over 90% existing and a lot of times only 2-3% new. So there is the expense of back capturing information. There will be an initial major back capture of data , then a small ongoing modification and recapturing on information as some areas are remodeled or refurbished or new assets come on stream.
Gathering of Data processes
Method 1. Go on site, inspect and measure for quantity & quality and put the information into the AMIS
This is a costly process as accurate surveying requires consistency. The cost of competent surveyors accessing all the properties and measuring them is quite costly.
There are issues with naming conventions of spaces and locations that require QA (Quality Assurance) procedures to ensure good data. Also this method only does physical spaces, not necessarily equipment & service systems.
I use a comparative example in Accuracy of Data from Physical Survey compared to Extraction from BIM
Method 2. Measure from plans and other docs for quantity and also survey existing condition for quality and put the information into the AMIS
This is a desktop exercise that can calculate quantities, a survey will still be required for quality. Quite efficient if you have good documentation of the buildings. This is a one off process, can include services and a measure for services (as long as Quantity Surveyor experienced with services (notoriously unreliable in this area).
Any small changes over time need to be remeasured from scratch. QA procedures/checks required for consistency.
Method 3. Extract from CAD plans & calculate quantity and also survey existing condition for quality and put the information into the AMIS
If you have 2D CAD (Computer Aided Drawing) documents (or possibly good quality Raster Scans that you can convert to vector CAD) then you can use Polylines to calculate Areas/perimeters of spaces (after drawing polylines).
Use Attributes ( import/export using Excel) to put in information about the building and export this information to AMIS.
There needs to be a validation process to ensure correct nomenclature is used for the data going into the AMIS. ( Refer to this post How to validate CAD Data after its exported )
For new buildings, if you have BIM’s (Building Information Model) then you can export CAD drawings and use these for your measure.
A quality survey still required for existing buildings (new buildings everything should be condition 1 (new)).
( Note- PDF exports are just normal 2D PDF’s. There is no attribute Data that can be extracted easily like the 3D PDF extraction to Excel as per BIM)
Method 4. Put into BIM & calculate quantity and also survey existing condition for quality and put the information into the AMIS

I think this is the best method. My reasons are:
- Accurate data directly from the model (ie quantities are as accurate as the drawn model- same as polylines in CAD above)
- You can extract more data with less input (eg Nett wall area of room instead of Gross wall area o room, can calculate accurate skirting lengths (by subtracting doors and openings from perimeter length))
- Automated process of extraction (not a one button process but not too onerous either)
- Automatically updates with alterations, so no need to re-calculate all quantities, these adjust to new spaces.
- If you put something into the Model, you can extract data about it.
- Validation process within Revit/RTV Reporter Pro tools so data going into AMIS is consistent.
- Add information incrementally. For back capture of existing buildings, initially only put in spaces and extract data, later can add services to model and then extract that data too.
- You can create 3D PDF’s with accessible viewable & extractable data to Excel- Good for giving to contractors for Preliminary measuring for Estimation. See 3D PDF’s and building data extraction to spreadsheet
For new assets there are usually BIM models. If this is the case, you can extract data directly from the model. This is good for current and future projects, as the documentation is in the appropriate format.
For existing buildings the process of creating the BIM’s floor plans from:
- Scanned images by either importing image & tracing over ( if imperial, change units and trace over then change to metric) or by converting the scans from Raster to Vector to CAD.
- CAD drawings by importing as Link and using Wall command with PICK LINE to select CAD walls, this creates a Revit wall. So you can quickly draw the floor plan.
A quality survey still required for existing buildings (new buildings everything should be condition 1 (new)).
- Speed up the tedious stuff and enjoy designing and documentation more
- Works in all versions of Revit
- Information to PROVE your increased speed
For an example of the process of the processes below see Revit asset data extraction for Asset Management Information System (AMIS) :
- Creating simple BIM models from scanned image plans
- validating the information
- Data Capture from the models and exporting to Database
For exporting to 3D PDF from Revit see How to use 3D PDF’s & Excel Macro’s to manage your assets part 3 of 3- Export from BIM
For 3D PDF visualisation & export to CSV see How to use 3D PDF’s & Excel Macro’s to manage your assets part 1 of 3
For Excel Macro Model Data management see How to use 3D PDF’s & Excel Macro’s to manage your assets part 2 of 3
[*1] An Asset Management Information System (AMIS) can be:
- Asset Information Storage and workorder processing and maintenance scheduling as well as accounts and document management systems ( Example OpenMAINT).
- Modelling & analytics tool, usually with a Database of information on which it can run predictive analytics such as Value of Assets, Ballpark Cost Estimates for types of work on specific assets and has a Table of BaseLifes for Elements. Some can add deferred maintenance modelling & future/present costs and value of whole buildings at different points in time (Example SPM Assets).
- There are other AMIS systems that do both of the above or similar function.
Related Posts

Revit notes, keynotes and detail notes
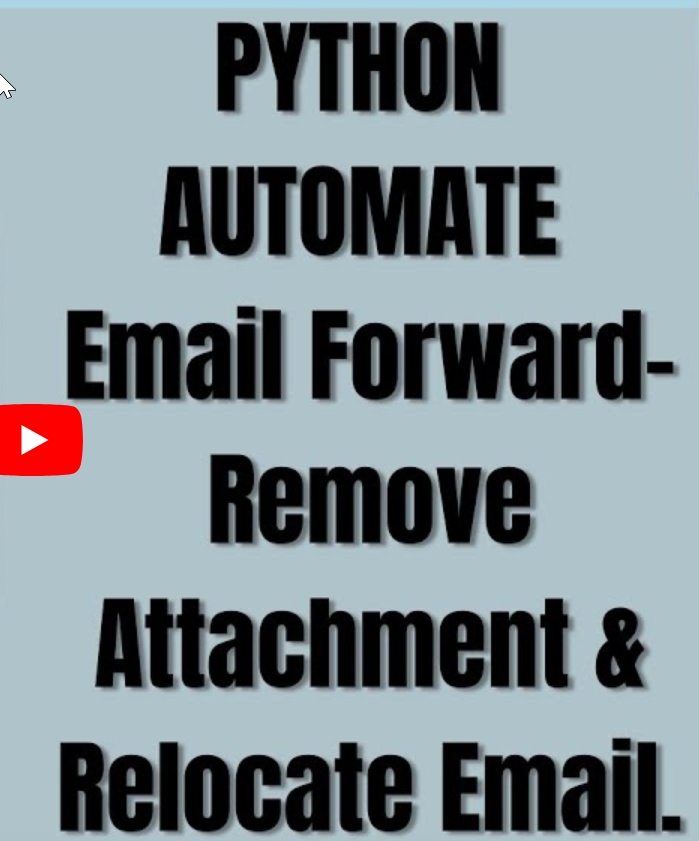
Python AUTOMATE Email Forward Remove Attachment & Relocate Email
